Aluminum, as a lightweight and high-strength metallic material, is widely used in various industries due to its excellent physical and chemical properties. This paper will delve into the basic properties, different types, industry applications and machining methods of aluminum to help readers better understand the importance of aluminum in manufacturing.
Ⅰ. Aluminum Overview
1. What is Aluminum?
Aluminum is a metallic element with the symbol Al, atomic number 13, and belongs to group IIIA.
Aluminum is a silvery-white light metal that is ductile, has good electrical and thermal conductivity and corrosion resistance, and is commonly used in the manufacture of various components.
It has a density of 2.7 g/cm³, a melting point of 660°C, and a boiling point of 2327°C.

2. Composition of Aluminum
Pure aluminum has an aluminum content of at least 99.0%, and other elements must meet specific limits.
Based on its composition, aluminum can be classified as premium pure aluminum, industrial high purity aluminum and industrial pure aluminum. Of these, premium pure aluminum has an aluminum content between 99.93% and 99.999%, while industrial high purity aluminum is 98% to 99.7%.
In practice, different alloying elements, such as copper, magnesium, zinc and silicon, can be added to aluminum, thus changing its organizational structure and properties and making it suitable for a wide range of processing and casting applications.
3. Sources of Aluminum
The smelting process of aluminum mainly includes bauxite extraction and electrolysis. Bauxite ore is calcined at high temperature to extract bauxite slurry, and then electrolysis is used to obtain metallic aluminum.
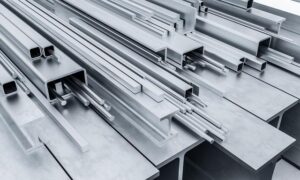
4. Advantages of aluminum materials
Aluminum’s light weight and resistance to corrosion are two outstanding features of its performance. In addition, it is characterized by the following features.
- Excellent thermal conductivity
- High corrosion resistance
- Light weight
- Easy to process
- Good strength
- Good ductility
- Non-toxic
- Low temperature resistance
- Conductive
- Reinforceable
- Non-magnetic
- Ductile
Ⅱ. Different types of aluminum
According to different criteria, aluminum can be classified into the following types:
- Name: Pure Aluminum
- Definition: Aluminum containing more than 99% aluminum.
- Elemental content: Contains only aluminum.
- Characteristics: Low strength, good ductility.
- Name: Aluminum Alloy
- Definition: Alloy of aluminum with other metal elements.
- Elemental content: Contains copper, zinc, magnesium, etc.
- Characteristics: High strength, good corrosion resistance.
Ⅲ. Properties of Aluminum
Name | Description | Common Aluminum | Advantages | Density Range | Applications |
Pure Aluminum | Content exceeds 99% | 1060 Aluminum | Excellent conductivity and ductility | 2.70 g/cm³ | Electrical wires, electronics |
Aluminum Alloy | Aluminum combined with other metals | 6061 Aluminum | High strength, excellent corrosion resistance | 2.70-2.80 g/cm³ | Aerospace, transportation |
Ⅳ. Industry Applications of Aluminum
Aluminum has a wide range of applications in the following industries:
Aerospace
Aluminum alloys are widely used in aircraft fuselages, airfoils and engine components. Its lightweight property reduces the weight of aircraft, improves fuel efficiency and increases the load.
Automotive
Aluminum alloys are used in automobiles for engine parts, body structures, wheels and frames. Compared with traditional steel, aluminum alloys are lighter, stronger and corrosion-resistant, helping to improve fuel economy and reduce exhaust emissions.
Construction and Decoration
Because of its corrosion resistance and light weight, aluminum is often used to manufacture windows, doors, curtain walls, profiles, ceilings and decorative panels.
Electronics
Aluminum is used in electronic equipment housings, heat sinks, components and circuit boards, with good thermal and electrical conductivity, effective heat dissipation and signal transmission.
Packaging
Aluminum is widely used in the field of packaging, mainly used in food, beverage, pharmaceutical and other industries. Aluminum packaging is lightweight, inexpensive and environmentally friendly. In addition, aluminum profiles are also used to make the frame of automatic packaging equipment and its components, with anti-corrosion, anti-static and not easily deformed.
Other fields
Aluminum is also used in shipbuilding, railroad transportation, sports equipment, solar energy industry and home decoration, showing its wide application as an important metal material.
Ⅴ. Common Aluminum Parts Processing and Manufacturing Methods
Common machining methods for aluminum parts are mainly the following 3 kinds:

CNC machining
Suitable for complex shape parts, high precision.
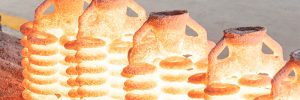
Investment casting
Suitable for small batch production, capable of producing complex shapes.
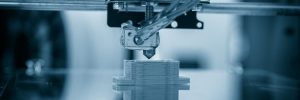
3D printing
Suitable for rapid prototyping with high flexibility.
The specific choice of processing method depends on the budget cost and the appearance and performance requirements of the final product. It is worth mentioning that Allied Metal provides one-stop aluminum parts machining service, which can ensure high quality and timely delivery.
Contact us immediately for processing details
Ⅵ. Advantages and Disadvantages of Aluminum in Manufacturing
Advantages
Lightweight: reduces transportation costs.
High strength: for structural applications.
Corrosion resistance: extends service life.
Disadvantages
Relatively high cost: aluminum is costly compared to other materials.
High thermal conductivity: may not be favorable for temperature control in some applications.
Ⅶ. Summary
Aluminum’s unique characteristics as a versatile material make it a key player in several industries. Whether it is in the aerospace, automotive industry or construction, the applications for aluminum are promising. Understanding the properties, types and processing methods of aluminum is important in selecting the right material and process.