CNC (Computer Numerical Control) machining is widely used in modern manufacturing for its precision and efficiency. However, even with advanced technology, various problems can arise during the process that affect quality and productivity.
Understanding these issues and how to fix them can help optimize production and improve product outcomes. Below, we’ll go over common CNC machining problems and their solutions.
1. Workpiece Positioning and Clamping Issues in CNC Machining
Problem:
If the workpiece isn’t positioned correctly or clamped securely, it can lead to errors or even scrap the entire part, especially with complex shapes or large workpieces.
Solution:
Use the appropriate fixtures and positioning devices. Standard-shaped workpieces often have readily available fixtures, while custom fixtures might be needed for more complex shapes. Always check the positioning accuracy before machining to avoid any costly mistakes.
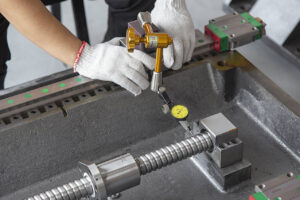
2. Tool Selection and Wear in CNC Machining
Problem:
Incorrect tool selection or excessive tool wear can result in rough surfaces, inaccurate dimensions, and burrs. Failing to replace worn tools on time can also reduce the lifespan of the machine.
Solution:
Select the right tool based on material hardness: Harder materials need stronger, more wear-resistant tools.
Set up a tool maintenance schedule: To regularly check for wear and replace tools as needed. This improves both product quality and machine lifespan.
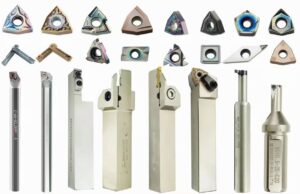
3. Machine Vibration During CNC Machining Process
Problem:
Machine vibration is a frequent issue that can lower precision, wear out tools faster, and negatively impact surface finish.
Solution:
- Make sure the machine is in good condition
- Regular maintenance
- Proper tool selection
- Correct selection of cutting parameters
- Using anti-vibration devices
- Using specialized software can further minimize the problem.
For high-quality CNC machining services, Allied Metal offers a one-stop solution from machining to surface finishing. Whether your workpiece is simple or complex, Allied Metal ensures efficient and reliable results.
4. Incorrect Cutting Parameters
Problem:
Improper settings for cutting speed, feed rate, or depth of cut can lead to poor results, wasted time, and even damaged tools or workpieces.
Solution:
Set cutting parameters based on the material, tool type, and machining requirements. Always do a test run before full production to fine-tune these settings. Monitor the parameters closely during production to ensure stability and efficiency.
5. Programming Errors
Problem:
Errors in CNC programming can result in machining failure or serious deviations from design, affecting not just a single workpiece but potentially the entire production run.
Solution:
Use reliable CAD/CAM software for programming, and always run a simulation before actual machining to catch any potential errors. Have experienced engineers review the program to ensure everything is correct.
6. Poor Surface Finish
Problem:
Even if the dimensions are accurate, a rough surface finish can lower the overall quality of a product. This is often due to dull tools, machine vibrations, or poor lubrication.
Solution:
To improve the surface smoothness of CNC machined workpieces, the following work should be done:
- Keep tools sharp and replace them when necessary.
- Regularly check the machine’s alignment and stability.
- Good lubrication and maintenance are also essential for improving surface quality.
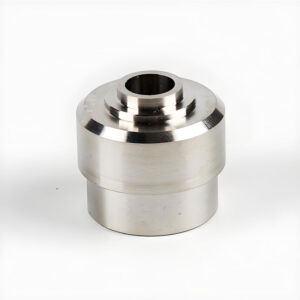
7. Taper Issues in Workpieces
Problem:
When one end of the workpiece is larger than the other, this taper issue usually comes from an uneven machine setup or excessive cutting depth. This is particularly common in longer workpieces.
Solution:
Use a spirit level to ensure the machine is properly leveled. Controlling the cutting feed and depth will also help prevent significant tapering.
Conclusion:
CNC machining is precise, but any issue can affect the final result. By recognizing common problems like positioning errors, tool wear, vibration, or programming mistakes, you can take action to improve both efficiency and quality. Regular maintenance and careful monitoring of the process are key to preventing these issues and maintaining smooth production.