Catalog:
Essential Tips for Selecting a CNC Machining Supplier and Optimizing Production
- Tony
- March 4, 2025
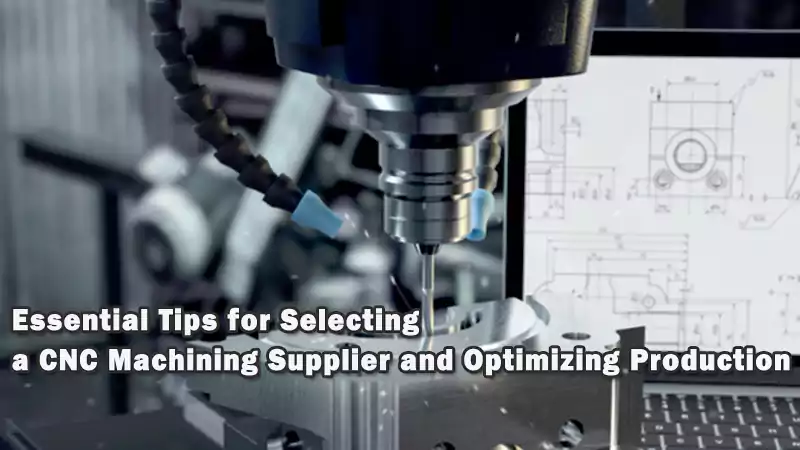
In today’s competitive manufacturing industry, by choosing the right machining solutions, optimizing production processes and working with effective CNC machining suppliers, companies can achieve significant improvements in cost and productivity.
In this article, we will discuss key strategies to improve CNC machining efficiency and help you choose the right CNC machining supplier to increase productivity and reduce costs.
1. Key Strategies for CNC Machining Supplier to Improve Efficiency
Core Factors Affecting CNC Machining Efficiency

CNC machining efficiency is influenced by factors such as equipment technology, process design, personnel operations, and management. Optimizing these aspects can significantly boost productivity.
How Advanced CNC Equipment Enhances Machining Efficiency?
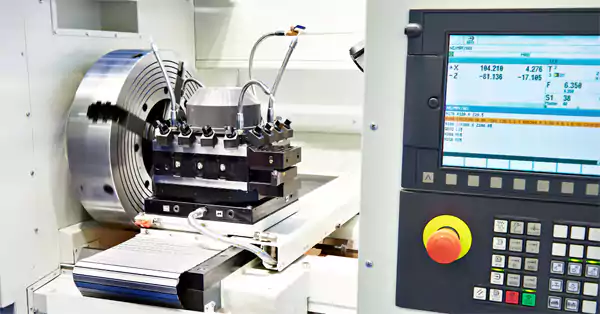
Modern CNC machines, especially 5-axis models, reduce adjustment time during machining, improving both accuracy and productivity. CNCs with higher control precision can speed up machining and shorten production time.
CNC Machining Supplier Lean Manufacturing
Lean manufacturing methods improve productivity by cutting waste and optimizing workflows. By minimizing raw material waste and unnecessary delays, Lean principles can be applied across all stages of production.
2. How to Choose the Most Suitable CNC Machining Supplier?
Evaluate equipment and capabilities of CNC machining supplier

The first step is to evaluate the equipment of the CNC machining service provider. Suppliers with state-of-the-art machine tools, such as five- or three-axis CNC machines, can provide accurate and efficient machining of a wide range of complex parts.
Assessing Quality Control Systems
Ensure the supplier has a robust quality management system, like ISO 9001 certification. This guarantees high-precision machining and reduces the likelihood of defects.
Reviewing Delivery and Supply Chain Reliability
A supplier’s ability to meet deadlines and manage inventory is crucial. Review their delivery history and flexibility to ensure timely and quality deliveries.
3. CNC Programming Optimization for Increased Efficiency
Leveraging Automated CNC Programming Software
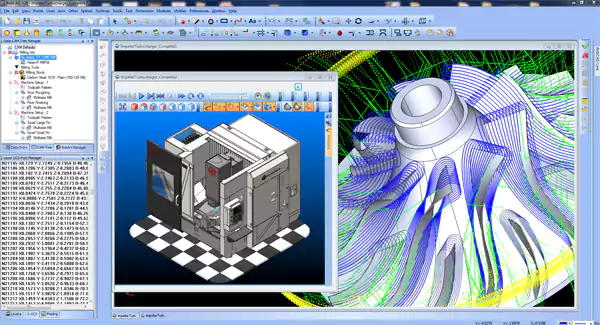
Automation in CNC programming can significantly enhance efficiency by reducing the need for manual intervention.
CAD/CAM systems seamlessly integrate with CNC machines, allowing CNC machining manufacturers to automate programming tasks and improve precision, thus speeding up production timelines.
Tool Path Optimization: Boosting Speed and Quality

Optimizing tool paths ensures that CNC machines operate at peak efficiency, reducing idle time and improving cutting quality.
By refining tool trajectories, CNC machining manufacturers can minimize machining time, extend tool life, and reduce material waste, ultimately enhancing both speed and product quality.
AI-Powered CNC Programming: Transforming Efficiency

The integration of AI in CNC programming is revolutionizing the industry.
By analyzing real-time data, AI systems can predict potential issues, optimize machining paths, and improve material usage, ensuring that CNC machining providers can stay ahead of market demands while maintaining efficiency.
4. How to Reduce Costs through CNC Machining?
Material Selection and Process Optimization
Choosing the right materials and optimizing machining processes lowers production costs. Proper parameters and design improve part quality while reducing waste.
Automation to Reduce Labor Costs and Boost Productivity
Automation reduces labor costs and boosts productivity by speeding up production, minimizing errors, and cutting downtime.
Efficient Supply Chain Management
Effective supply chain management reduces inventory and logistics costs. Accurate inventory and strong supplier ties lower operating costs and ensure a steady supply.
5. Challenges and Solutions for CNC Machining Different Materials
Machining Aluminum, Titanium, and Carbon Fiber
Machining requirements vary by material.

While aluminum alloys are relatively easy to machine, titanium alloys require specialized tools and techniques due to their hardness, and carbon fiber needs specific cutting tools to prevent breakage during machining.
Optimizing Tool Selection and Cutting Parameters
Choosing the right cutting tools and optimizing parameters are critical to improving CNC machining efficiency.
For instance, titanium alloys need slower cutting speeds, while carbon fiber requires specific tools for optimal results.
Surface Treatment and Its Impact on Machining Quality
Surface treatments enhance durability, corrosion resistance, and precision in CNC machining.

For example, anodizing aluminum improves the strength of the material, making it more durable and capable of withstanding wear, which in turn improves overall machining accuracy and efficiency.
6. How to Choose the Right Custom Part Machining Solution?
When to Use 5-Axis CNC Machining?
5-axis CNC machining is best for complex parts, tight spaces, or high-precision requirements. Its ability to machine from multiple directions at once reduces clamping and boosts accuracy and efficiency.
Advantages of 3-Axis CNC Machining
3-axis CNC machining works well for flat or simple parts. It is cost-effective and ideal for producing common, straightforward parts.
Multi-Axis Machining’s Role in Production Strategies
The choice of multi-axis machining influences production strategies. CNC Machining Manufacturers can optimize schedules, accuracy, and lead times based on customer needs and machining requirements.
7. How do I assess the quality management system of a CNC machining supplier?
Essential Quality Control Tools:
Quality control is essential for ensuring CNC machining accuracy.
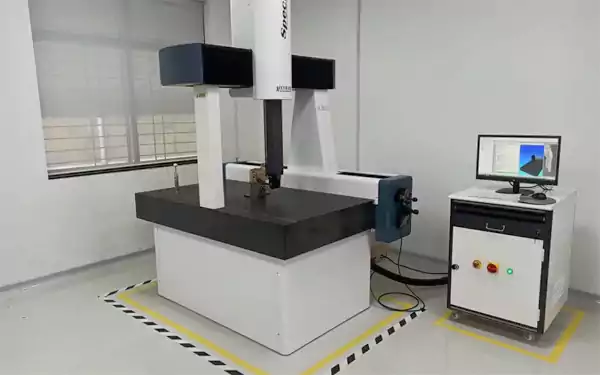
Using advanced tools like Coordinate Measuring Machines (CMM) and Optical Measuring Instruments allows suppliers to meet precise customer requirements.
Precision Control of Tolerances and Consistency:
With strict process control and efficient equipment, CNC suppliers can precisely manage machining tolerances to guarantee consistency and high accuracy for each part.
Quality Traceability and Inspection Reports:
A reliable traceability system is vital in CNC machining. Detailed inspection reports and process records help suppliers assure customers of the quality of each part.
8. Differences in Part Customization Across Industries
Aerospace: Precision and Lightweight Machining
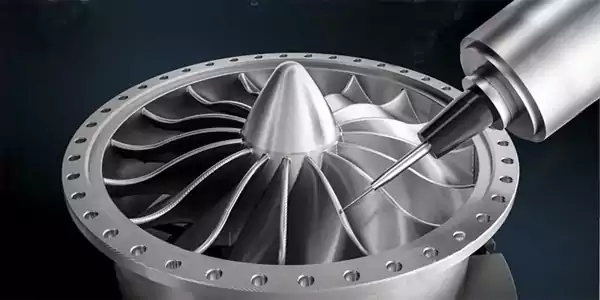
The aerospace industry demands high-precision and lightweight components, making custom CNC machining solutions essential for meeting strict safety and performance standards.
Medical Device Manufacturing: Tight Tolerances and Sterility

In medical device manufacturing, CNC machining is used to create highly precise parts such as surgical instruments and implants, which require stringent tolerances and sterility.
Automotive: High-Volume, Efficient Machining
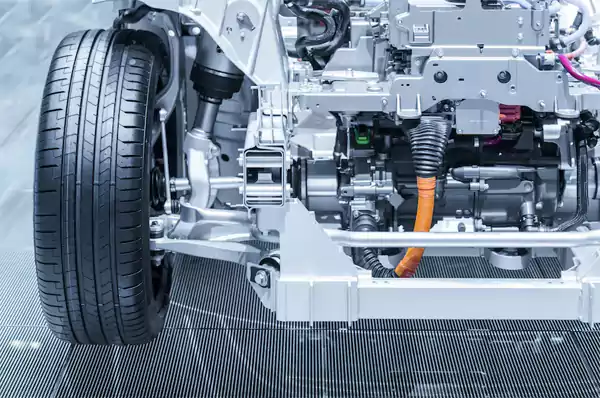
Automotive CNC machining focuses on high-volume production while maintaining precision and efficiency. This ensures that manufacturers can produce large quantities of high-quality parts while minimizing costs.
9. Smart Manufacturing and Industry 4.0: Future Trends for CNC Machining Supplier
IoT Integration in CNC Machining
IoT technology allows real-time remote monitoring and control of CNC machines, improving transparency and making maintenance and scheduling more efficient.
AI-Powered Predictive Maintenance
With AI-based predictive maintenance, potential issues are detected before they cause downtime, ensuring that production remains continuous and reducing maintenance costs.
Data-Driven CNC Machining for Enhanced Competitiveness
By leveraging big data, CNC machining providers can optimize their processes, reduce waste, and make better decisions, ultimately boosting their competitiveness in the global market.
10. Conclusion
Looking ahead, the CNC machining industry is poised for growth driven by advancements in automation, smart manufacturing technologies, and a commitment to sustainability. CNC machining service providers must prioritize efficiency, precision, and eco-friendly practices to deliver high-quality, cost-effective, and custom parts while staying competitive in an evolving marketplace.
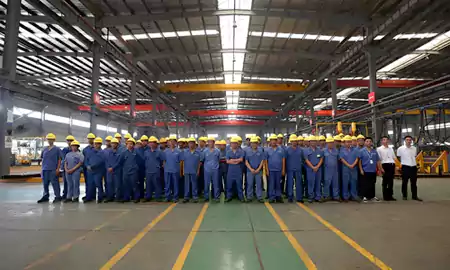
Hi, I'm Tony!
I’m a CNC machining specialist at Allied Metal with over 20 years of experience in this field. We offer cost-effective machining services from China.
Contact us now to get a free quote for your project!
Let’s collaborate! Turn ideas into products!